Interview of Associate Professor Ryo TANAKA
On-demand Crosslinking of Rubber Facilitates Previously Impossible Ways of Recycling
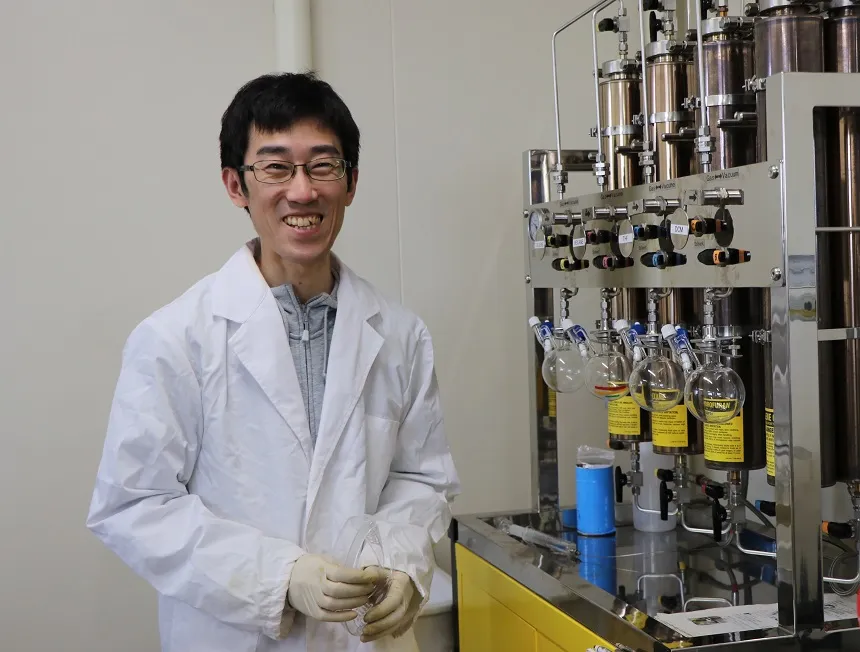
Program | JST Strategic Basic Research Programs (PRESTO) | Researchers selected in the FY | 2022 |
---|
Tailoring Catalysts to Make the Ideal Polymer Structure
My specialty is synthetic polymer chemistry. All materials—including, for that matter, we humans—include polymers, and I study the synthesis of polymers using organic chemistry. My focus is on polyolefins and polydienes, which are hydrocarbon-based polymers used in things like plastics, rubber, wrapping films, car chassis.
These materials have become demonized in recent years, for instance in the uproar surrounding ocean plastic pollution. But their advantages—they are extremely light and easy to handle—far outweigh their disadvantages, so it is not feasible, for now at least, to completely exclude them from human life. The only way to minimize these materials is to reduce the volume required to make the things they’re used in; we should pursue developments that achieve the desired functionality and lifespan with smaller quantities of synthetic polymers. In addition, we should find ways to enable recycling of recoverable materials with as little hassle as possible.
In general, synthetic polymers have a somewhat repeating structure. These compounds are represented in chemical formulas as very simple structural repeats, but they are not necessarily connected in the same way. For instance, physical properties such as strength and durability can vary greatly depending on the length and distribution of the repeating structure.
Polymers are synthesized by linking monomers (low-molecular compounds) together in a polymerization reaction, and this requires catalysts. My work involves designing their structures and developing catalysts that result in polymers that are just right.
Undoable Polymer Cross-Links Will Make Rubber Re-moldable and Recyclable
Making rubber requires hydrocarbon polymers consisting of carbon and hydrogen to be cross-linked. This makes the polymers connect in a network structure, which gives the material strength. The current method of cross-linking, which uses sulfur, has a disadvantage: once the network has been established, the cross-link is permanent and the polymer cannot be undone, and this permanency of cross-linking has long been an obstacle to recycling.
If the cross-link could be undone and redone—i.e., if used rubber could be remolded—it would be recyclable. Currently, even if used tires are collected, incineration is the only way to dispose of them; they can’t be reconstituted as tires or turned back into rubber, and the only real method of reusing tires was to grind them into rubber powder.
I was inspired to apply for the Japan Science and Technology Agency’s 2022 PRESTO Strategic Basic Research Program for my project, “Development of Recyclable Commodity Rubber Materials with the Degradation Initiating from Crosslinking Points,” because we had developed a compound that uses boron instead of sulfur and results in a rubber whose polymer cross-links can be undone. Apart from the cross-links, the main structure is exactly the same as regular rubber, so the material is sufficiently strong and can be freely changed in length.
The material displays virtually the same level of functionality after undoing and re-doing the polymer cross-links. However, for example, some tires are reinforced with carbon black, a carbon powder, and its presence makes it difficult to directly recycle the used tire back into rubber. The ability to turn the polymer back into raw material (e.g., ethylene) may be a roundabout way of recycling, but it is still an improvement on the current situation. Still, there are some challenges yet to overcome in turning polymers back into raw materials, and we look forward to tackling these.
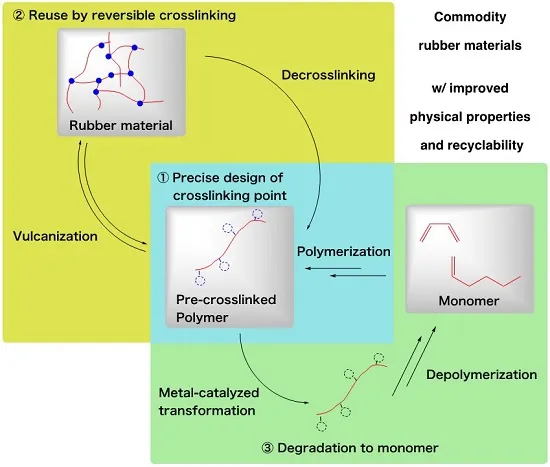
How rubber can be recycled by undoing and re-doing the polymer cross-links
Cross-disciplinary Interaction and New Frontiers: The Joys of Polymer Research
The idea of cross-linking with boron is not unusual. Who remembers the popular kids’ experiment of adding borax, which contains boron, to laundry starch to make slime? Laundry starch is a polymer—polyvinyl alcohol—and mixing it with boron is a simple exercise in cross-linking that results in a soft, elastic slime. Cross-linking is easy in this case because there are many points boron can grab on to.
Conversely, the hydrocarbon-based polymers that make up rubber have nothing for boron to bond with, making it very difficult to crosslink by mixing the polymer with borax directly. Our approach is to focus closely on the design of the monomer and catalyst, which enables the introduction of boron into hydrocarbon-based polymers during initial synthesis. So far, we are the only ones in the world to achieve such reactions.
Furthermore, while most rubber material compounds have unorganized structures, the material we have developed has the potential to be a stronger rubber because its cross-linking points are distributed and the network is uniform. By participating in the PRESTO program, we have benefited from input from people who study rubber from a physical perspective, and we are now in pursuing joint research aimed at developing practical applications for our material.
The study of polymers is extremely diverse; making good products attracts the interest of people in a variety of other fields, and their input leads to fresh developments. Working in this field is a rewarding experience because it opens up frontiers that I have never encountered before.